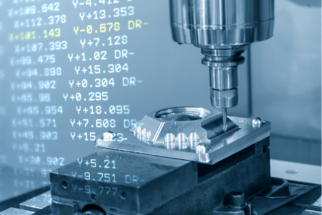
CMC milling in focus
How much do you know about 3D printing’s subtractive rival, CNC milling?
As one of the key services that we provide, here at Special Metals, we have detailed knowledge of this advanced metal fabrication technique. And to help you decide whether CNC milling is the right option for your project, here we take a closer look at exactly what it is and how it works.
What is a CNC milling machine?
Essentially, a CNC milling machine is a fully-automated piece of machinery, which uses computer numerical control (i.e. CNC) to produce a new metal part. CNC is a series of code. And once inputted into the machine, it tells it exactly how to move to cut the metal and create the product.
Unlike a 3D printing machine, which uses an additive process to add material, CNC milling machines do the opposite. They subtract or remove material until the desired product has been manufactured. And as a reliable and effective tool, they’re now found in all good metal fabrication shops.
How does the CNC milling process work?
Step 1: Design
The CNC milling process starts by designing the metal part in CAD (Computer-Aided Design) software. By using the client’s specification, a 3D model or virtual representation is created – including details of the size, dimensions and properties of the final product.#
Step 2: Translation
Some CAD software automatically translates this 3D model into the necessary code. But if not, the CAD model will need to be fed into CAM (Computer-Aided Manufacturing) software.
In essence, this software prepares the 3D model for fabrication and will:
- check the model for errors
- determine coordinates that will guide the cutting head
- choose the correct parameters for manufacture (i.e. cutting speed, revolution per minute)
- determine the nesting (i.e. the orientation of the part relative to the raw material)
All of this information is then translated into codes which the CNC milling machine can understand. The first code – G-code – instructs the machine how to move and determines the trajectory and speed of the cutting head. The second code – M-code – includes miscellaneous information that G-code overlooks, such as the use of coolant, necessary tool changes and program stops.
Step 3: Setting up the machinery
Once the code has been created, this is entered into the machine controller.
CNC milling machines work automatically and some advanced models can even change tools on-the-go, without having to stop the manufacturing process. But before this process can begin, the machine still needs to be set-up manually. For example, the operator will need to fix the workpiece to the worktable and attach the milling tools to the spindle of the machine.
Step 4: Producing the parts
Once the machine has been given the green light to start, it uses a rotating tool to cut away the metal. And by following the inputted code, and continuously cutting, the desired product is created.
Is CNC milling the right option for my project?
This depends on the nature of your desired metal part.
CNC milling machines have fantastic capabilities and offer an efficient and reliable way of creating intricate, complex products. But they can be a little more expensive than other fabrication methods. And for relatively simple metal parts, these other methods can often produce the same results.
Therefore, if you’re unsure of whether CNC milling is right for your project, the best option is to get in touch with our experts. As a UK leading metal fabrication company, we have several CNC milling machines on-site and boast significant experience in this area. We’ve worked on countless CNC milling projects in the past and can advise on the best fabrication techniques to create your part.
All you have to do is give us a call on +86-755-29936699 to speak to a member of the team. Alternatively, you can send an email to inquiry.mp@professionalmanufacturing.com and we’ll respond as soon as possible.
Leave a response
Your email address will not be published. Please enter your name, email and a comment.