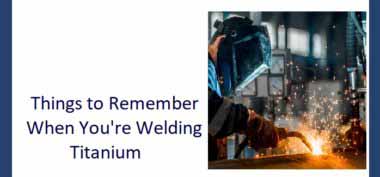
Things to Remember When You’re Welding Titanium
Titanium is almost legendary in popular culture for its strength and resistance to corrosion and damage – and for good reason. This extremely durable metal has one of the the highest strength-to-weight ratios of any metal, and is commonly used in producing lightweight, strong performance alloys for aerospace engineering or spacecraft use.
In addition to this, it’s highly resistant to corrosion, thanks to a passivation layer of titanium oxide that spontaneously forms in contact with the air, making titanium almost as corrosion-resistant as platinum, and serving it well for use in marine applications. However, titanium does react with many gasses at high temperatures, but still below its melting point, which leads to a series of challenges when welding titanium. If not adequately shielded with inert gas, the welded titanium will react with the air to form brittle compounds, and the weld will fail.
What are the Advantages of Titanium?
As mentioned above, titanium is a very strong, lightweight metal which resists corrosion thanks to a thin passivation layer. When alloyed with other metals, titanium lowers the weight of the resulting alloy while greatly boosting the strength, and even when used in its pure form, the metal’s durability and chemical properties make it very desirable in many demanding applications.
Why is Titanium So Hard to Weld?
Titanium is relatively unique among metals in that it begins to combust at lower temperatures than its melting point. At high temperatures, titanium will react with oxygen in the air to form titanium dioxide, and with nitrogen to form titanium nitride. Therefore, if a welder attempts to weld titanium in the normal atmosphere of the welding shop, the weld (which must reach temperatures above the melting point of titanium in order to work) will be contaminated with brittle titanium compounds, becoming weak and possibly cracking during cooling. In either case, the weld will not be successful, and the component may be ruined. This has led many welders to declare titanium “too difficult” to be worth bothering with, but with the right preparations, titanium welding can result in a stronger, more durable weld than with any other metal – perfect for demanding applications.
Things to Remember When Welding Titanium
When welding titanium, it’s important to keep a few things in mind to ensure a successful weld:
The Shielding Gas Is Crucial
Any attempt at welding titanium in the normal atmosphere of the welding shop will result in a failed weld, contaminated by the metal’s reaction with the air. Therefore, you’ll need to make use of an inert shielding gas, like argon, to make sure the weld is protected from the air during titanium welding.
Some welders even use a sealed environment full of inert gas when welding titanium – with glove-inserts and a titanium welding setup inside, but for the average shop this may be overkill. Experiment to find a welding option that suits your facilities and your needs!
The Three C’s – Clean, Clean, Clean!
Even in an inert gas atmosphere, it’s possible to spoil a titanium weld by contaminating it with other things – oil from your fingers, any dust, dirt, paint, lubricants or cutting fluids, and any other materials which might be on the welding zone all contribute to weld failure and must be removed before the weld can begin. So remember: clean, clean, clean!
How to Spot a Brittle Weld in Titanium Welding
Different shops and different industries have varying standards for what counts as an unacceptable weld with titanium welding. A perfect weld is silver-coloured, and looks almost like frozen mercury – this indicates pure titanium, and a strong durable bond.
Straw-coloured welds indicate a small amount of contamination, and in the strictest industries, they may be ruled out as failed welds. Many applications, however, allow a straw-coloured weld or even a brown weld, the next step up.
As the weld becomes more contaminated with titanium compounds, the colour will continue to change, from silver to straw, to brown, then on to violet, dark blue, light blue, green, and finally grey or white with oxide flakes. This is the most badly affected weld and is a sign that the shielding used did not work at all.
Contact Special Metals UK for Titanium Today!
If you would like more information on titanium and titanium welding, or you’d just like to speak to an expert, you can call Special Metals UK on +86-755-29936699 or send us a message on our contact form to get in touch!
The experts at our head office have been the industry authority on working with special metals for decades, and can answer any questions you may have or provide any advice which you may need. Titanium is an extremely versatile and adaptable metal, with uses across a huge range of industries – its extremely high strength-to-weight ratio, excellent thermal operating range and great corrosion resistance mean that titanium is the ideal metal for use in demanding applications, but the challenges of welding it often lead fabricators and engineers to avoid it.
This is a real shame, since with the right preparation and technique, titanium welding provides incredibly strong, durable structures, like those used in deep-sea exploration vehicles or in nuclear power stations. Now that you know the ins and outs of titanium welding, you’ll be in a great position to start exploring the advantages of this incredible metal!
Get in contact with us on +86-755-29936699 or send us a message today to request a quote or place an order for titanium or titanium fabrication today!
Leave a response
Your email address will not be published. Please enter your name, email and a comment.